Superalloy machining
Superalloys - metal alloys, which reflect their complex alloyed structure, have become one of the main engineering materials for a long time. They feature extremely high elevated temperature strength, and therefore often are referred to as high-temperature superalloys (HTSA) or heat-resistant superalloys (HRSA). The history of superalloys started with the development of gas-turbine engines that required reliable materials for high operating temperature ranges. As a result of intensive research and progress in metallurgy, modern superalloys (SA) provide a long service life for working temperatures more than 1000°C.
Understandably, the largest superalloy consumers today are aero- and marine engine producers (Fig. 1). Superalloys are also very common in the medical industry, which effectively use them for prosthetic implants in orthopedic surgery. In addition, superalloys have become widespread in power generation and the oil and gas industries as crucial materials for essential parts of various devices.
Exceptional high-temperature strength and corrosion resistance are the undeniable advantages of superalloys. However, there are two sides to the coin: superalloys are not only highly priced, but their machinability is poor, which can pose challenges to manufacturing. The specific cutting force that characterizes the resistance of the material to chip removal and defines the mechanical load on a cutting tool is high for superalloys. Although the main difficulty is heat, superalloys have poor thermal conductivity. Elemental and loose chips, which are generally generated when machining superalloys, do not provide adequate heat dissipation from the cutting zone. A tendency to work hardening makes the situation worse.
The manufacturer deals with various SA workpieces: cast, wrought, sintered, etc. The workpiece fabrication methods also have an impact on machinability. For example, abrasiveness of forged workpieces higher that cast ones substantially lower in comparison with sintered workpieces.
Consequently, a cutting tool is under significant thermal and mechanical load, which dramatically reduces tool life. Therefore, in machining superalloys, the cutting speed directly connected with the heat generation during chip removal is considerably lower when compared to other common engineering materials such as steel or cast iron. The direct result of the cutting speed limitation is poor productivity. Hence, overcoming machining difficulties and increasing productivity are the main challenges for the manufacturer of SA parts.
According to ISO 513 standard, superalloys together with titanium alloys relate to the ISO S group application. Depending on the prevailing element, superalloys are divided into three types: iron (Fe), nickel (Ni) and cobalt (Co) based alloys. Machinability drops in the specified order; from the iron-based alloys, which can be compared with austenitic stainless steel, to cobalt-based alloys that represent the most hard-to-cut materials in the group.
Increasing efficiency of machining superalloys has become the focus of various scientific research and technological improvements. Their result was a significant advance in producing SA components. Manufacturing has effectively embraced new machining strategies and innovative methods of cutting coolant supply, such as high-pressure cooling (HPC), minimum quantity lubrication (MQL) and even cryogenic cooling has successfully been introduced. This has taken the productivity of machining superalloys to a new level. However, like in the case of titanium alloys, the key element for improving the productivity of SA machining is a cutting tool that directly removes material layers from a workpiece that produces chips. A cutting tool features the tool material and its geometry, which determines the tool’s triumph or its failure.
Today, coated cemented carbides are the most common materials for cutting tools for machining superalloys. The development of a carbide grade, in which strength and wear resistance will be mutually complemented is a tricky process that requires an appropriate carbide substrate, coating composition, and coating method. To the amazement of those who believe that the breakthrough possibilities in this direction are almost exhausted, cutting tool producers continue to create new effective carbide grades. Additionally, in machining superalloys, ceramics - another tool material that enables substantially increased cutting speeds – are already in active use.
If tool materials are connected mostly with material sciences and metallurgy, cutting geometry is more in the tool design field. Ensuring high-performance geometry requires deep engineering knowledge and technology skills. On the one hand, to minimize heat generation and work hardening, a positive rake angle, a large enough clearance angle, and a sharp cutting edge are needed. On the other hand, such a shape weakens the cutting edge that should withstand a considerable mechanical load. Therefore, the correct designed cutting-edge condition becomes a critical success factor. Sintered carbide inserts have the advantage of enabling complex chip forming and chip breaking shapes for insert rake faces. Today, computer modeling of chip formation and pressing processes using finite element methods provide an effective tool to optimize the shapes that are already in the design stage. In solid endmills, a variable pitch design results in improved vibration strength. Cutting edges of these endmills are produced by grinding operations, and to eliminate flaking and edge defects, strict adherence to technological process requirements is highly important.
Cutting tool manufacturers pay a lot of attention to improving their product portfolios intended for machining superalloys. ISCAR's news can be excellent indicative examples.
Carbide grade IC806, which had was introduced over the last few years for face grooving superalloys and austenitic stainless steel, was successfully adopted by ISCAR’s threading and deep drilling lines. This grade has a hard submicron substrate and PVD TiAlN/AlTiN coating with post-coating treatment according to ISCAR’s SUMO TEC technology. IC806 provides notable resistance to flaking and chipping and maintains reliable and repeatable results.
In machining superalloys by solid carbide endmills and exchangeable heads, grade IC902, which combines ultra-fine grain substrate and nano-layer PVD TiAlN coating, ensures extremely high wear resistance and prolongs tool life. This grade has demonstrated very good results in producing devices for replacement knee and hip joints that are made from difficult-to-cut cobalt-chrome alloys (Fig. 2).
ISCAR has significantly extended the range of products for ISO S applications made from various cutting ceramics such as silicon nitride, SiAlON, and whisker-reinforced grades. The newly introduced ceramic items have replenished both indexable inserts and solid endmills (Fig. 3).
The latest rake face designs F3M and F3P for ISO standard turning inserts are intended specifically for hard-to-machine austenitic stainless steel and superalloys (Fig. 4). Their positive rake-angle geometry reduces the cutting force and ensures smooth cutting action, while the set of deflectors on the rake face improves chip control. In ceramic double-sided inserts for turning and milling tools, ISCAR has added new chamfered and combined (chamfered and rounded) cutting-edge condition options for tough applications.
ISCAR has enriched the range of solutions intended for high-pressure cooling by new indexable cutter bodies and tool holders. For example, thermal shrink chucks with polygonal taper shanks, which have coolant jet channels along the central bore, have been replenished by the toolholder product line.
In conclusion, the need for increased productivity in machining HTSA is a continuous challenge for cutting tool manufacturers, and new effective tool developments are likely to come in the near future.
Understandably, the largest superalloy consumers today are aero- and marine engine producers (Fig. 1). Superalloys are also very common in the medical industry, which effectively use them for prosthetic implants in orthopedic surgery. In addition, superalloys have become widespread in power generation and the oil and gas industries as crucial materials for essential parts of various devices.
Exceptional high-temperature strength and corrosion resistance are the undeniable advantages of superalloys. However, there are two sides to the coin: superalloys are not only highly priced, but their machinability is poor, which can pose challenges to manufacturing. The specific cutting force that characterizes the resistance of the material to chip removal and defines the mechanical load on a cutting tool is high for superalloys. Although the main difficulty is heat, superalloys have poor thermal conductivity. Elemental and loose chips, which are generally generated when machining superalloys, do not provide adequate heat dissipation from the cutting zone. A tendency to work hardening makes the situation worse.
The manufacturer deals with various SA workpieces: cast, wrought, sintered, etc. The workpiece fabrication methods also have an impact on machinability. For example, abrasiveness of forged workpieces higher that cast ones substantially lower in comparison with sintered workpieces.
Consequently, a cutting tool is under significant thermal and mechanical load, which dramatically reduces tool life. Therefore, in machining superalloys, the cutting speed directly connected with the heat generation during chip removal is considerably lower when compared to other common engineering materials such as steel or cast iron. The direct result of the cutting speed limitation is poor productivity. Hence, overcoming machining difficulties and increasing productivity are the main challenges for the manufacturer of SA parts.
According to ISO 513 standard, superalloys together with titanium alloys relate to the ISO S group application. Depending on the prevailing element, superalloys are divided into three types: iron (Fe), nickel (Ni) and cobalt (Co) based alloys. Machinability drops in the specified order; from the iron-based alloys, which can be compared with austenitic stainless steel, to cobalt-based alloys that represent the most hard-to-cut materials in the group.
Increasing efficiency of machining superalloys has become the focus of various scientific research and technological improvements. Their result was a significant advance in producing SA components. Manufacturing has effectively embraced new machining strategies and innovative methods of cutting coolant supply, such as high-pressure cooling (HPC), minimum quantity lubrication (MQL) and even cryogenic cooling has successfully been introduced. This has taken the productivity of machining superalloys to a new level. However, like in the case of titanium alloys, the key element for improving the productivity of SA machining is a cutting tool that directly removes material layers from a workpiece that produces chips. A cutting tool features the tool material and its geometry, which determines the tool’s triumph or its failure.
Today, coated cemented carbides are the most common materials for cutting tools for machining superalloys. The development of a carbide grade, in which strength and wear resistance will be mutually complemented is a tricky process that requires an appropriate carbide substrate, coating composition, and coating method. To the amazement of those who believe that the breakthrough possibilities in this direction are almost exhausted, cutting tool producers continue to create new effective carbide grades. Additionally, in machining superalloys, ceramics - another tool material that enables substantially increased cutting speeds – are already in active use.
If tool materials are connected mostly with material sciences and metallurgy, cutting geometry is more in the tool design field. Ensuring high-performance geometry requires deep engineering knowledge and technology skills. On the one hand, to minimize heat generation and work hardening, a positive rake angle, a large enough clearance angle, and a sharp cutting edge are needed. On the other hand, such a shape weakens the cutting edge that should withstand a considerable mechanical load. Therefore, the correct designed cutting-edge condition becomes a critical success factor. Sintered carbide inserts have the advantage of enabling complex chip forming and chip breaking shapes for insert rake faces. Today, computer modeling of chip formation and pressing processes using finite element methods provide an effective tool to optimize the shapes that are already in the design stage. In solid endmills, a variable pitch design results in improved vibration strength. Cutting edges of these endmills are produced by grinding operations, and to eliminate flaking and edge defects, strict adherence to technological process requirements is highly important.
Cutting tool manufacturers pay a lot of attention to improving their product portfolios intended for machining superalloys. ISCAR's news can be excellent indicative examples.
Carbide grade IC806, which had was introduced over the last few years for face grooving superalloys and austenitic stainless steel, was successfully adopted by ISCAR’s threading and deep drilling lines. This grade has a hard submicron substrate and PVD TiAlN/AlTiN coating with post-coating treatment according to ISCAR’s SUMO TEC technology. IC806 provides notable resistance to flaking and chipping and maintains reliable and repeatable results.
In machining superalloys by solid carbide endmills and exchangeable heads, grade IC902, which combines ultra-fine grain substrate and nano-layer PVD TiAlN coating, ensures extremely high wear resistance and prolongs tool life. This grade has demonstrated very good results in producing devices for replacement knee and hip joints that are made from difficult-to-cut cobalt-chrome alloys (Fig. 2).
ISCAR has significantly extended the range of products for ISO S applications made from various cutting ceramics such as silicon nitride, SiAlON, and whisker-reinforced grades. The newly introduced ceramic items have replenished both indexable inserts and solid endmills (Fig. 3).
The latest rake face designs F3M and F3P for ISO standard turning inserts are intended specifically for hard-to-machine austenitic stainless steel and superalloys (Fig. 4). Their positive rake-angle geometry reduces the cutting force and ensures smooth cutting action, while the set of deflectors on the rake face improves chip control. In ceramic double-sided inserts for turning and milling tools, ISCAR has added new chamfered and combined (chamfered and rounded) cutting-edge condition options for tough applications.
ISCAR has enriched the range of solutions intended for high-pressure cooling by new indexable cutter bodies and tool holders. For example, thermal shrink chucks with polygonal taper shanks, which have coolant jet channels along the central bore, have been replenished by the toolholder product line.
In conclusion, the need for increased productivity in machining HTSA is a continuous challenge for cutting tool manufacturers, and new effective tool developments are likely to come in the near future.
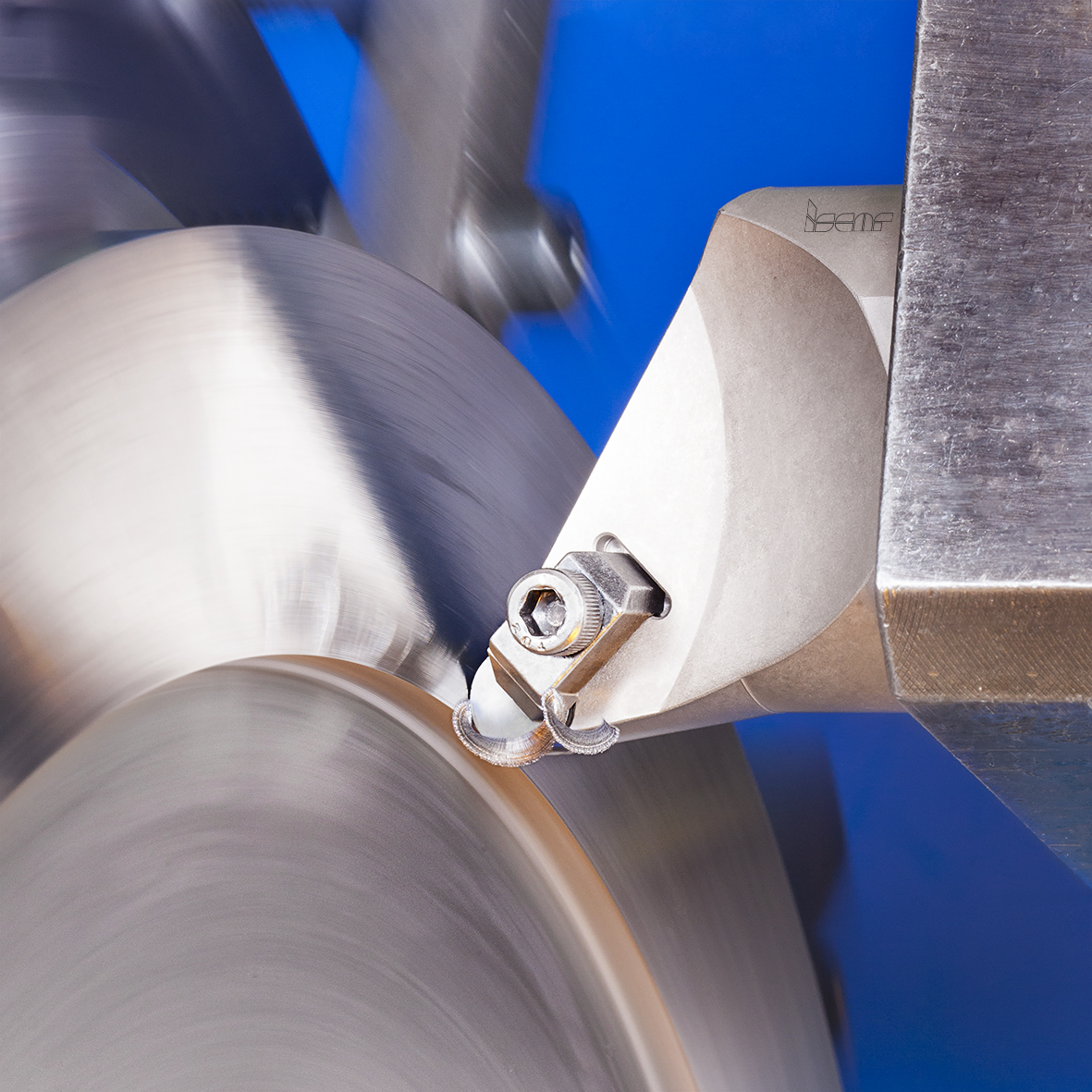
[Fig. 1- – Superalloys are the key materials for turbojet and turboprop engines of modern aircrafts. Jet engine blisk machined with ISCAR's CUT-GRIP systems. ]
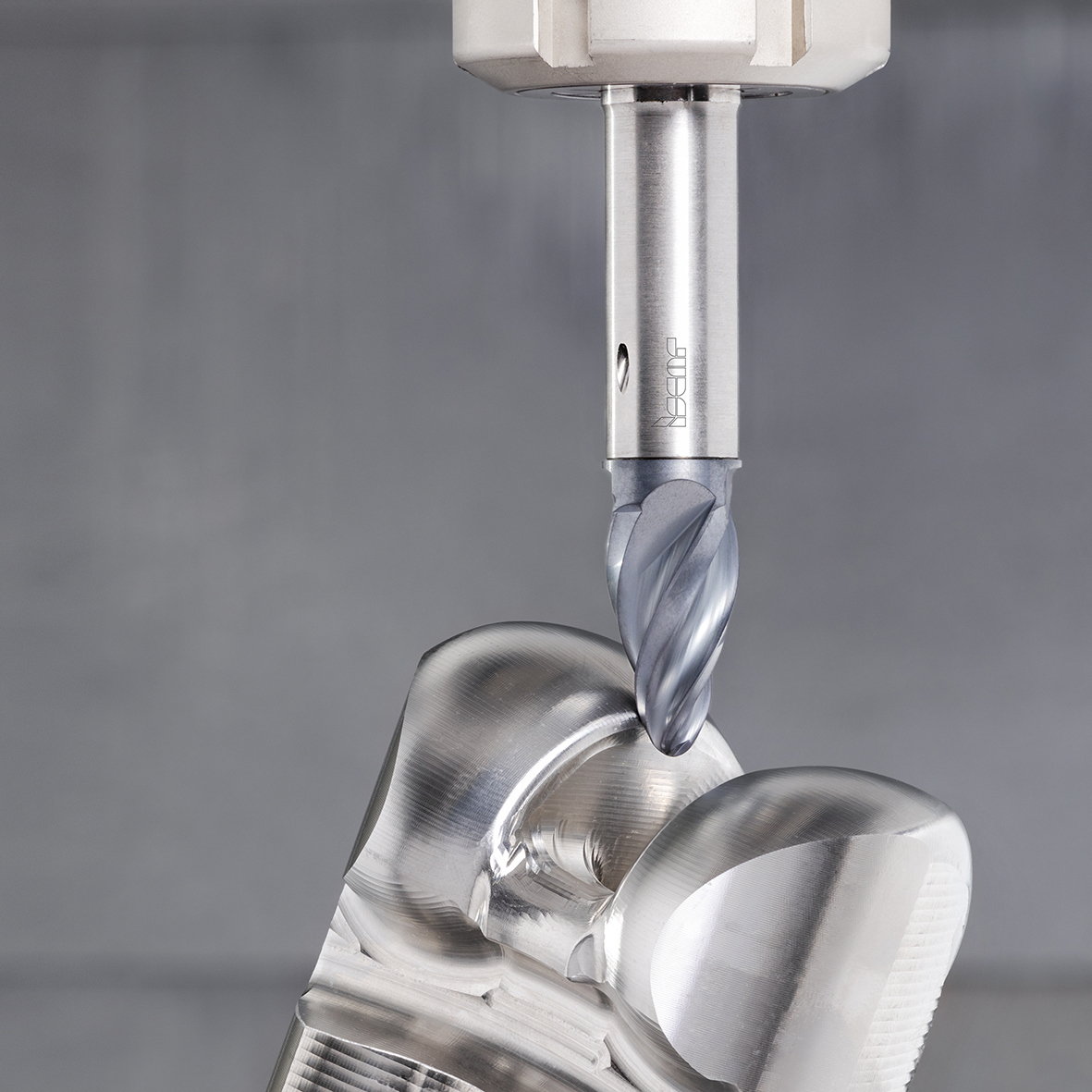
[Fig. 2- – Machining a femoral knee implant component with a MULTI-MASTER endmill and exchangeable taper barrel head.]
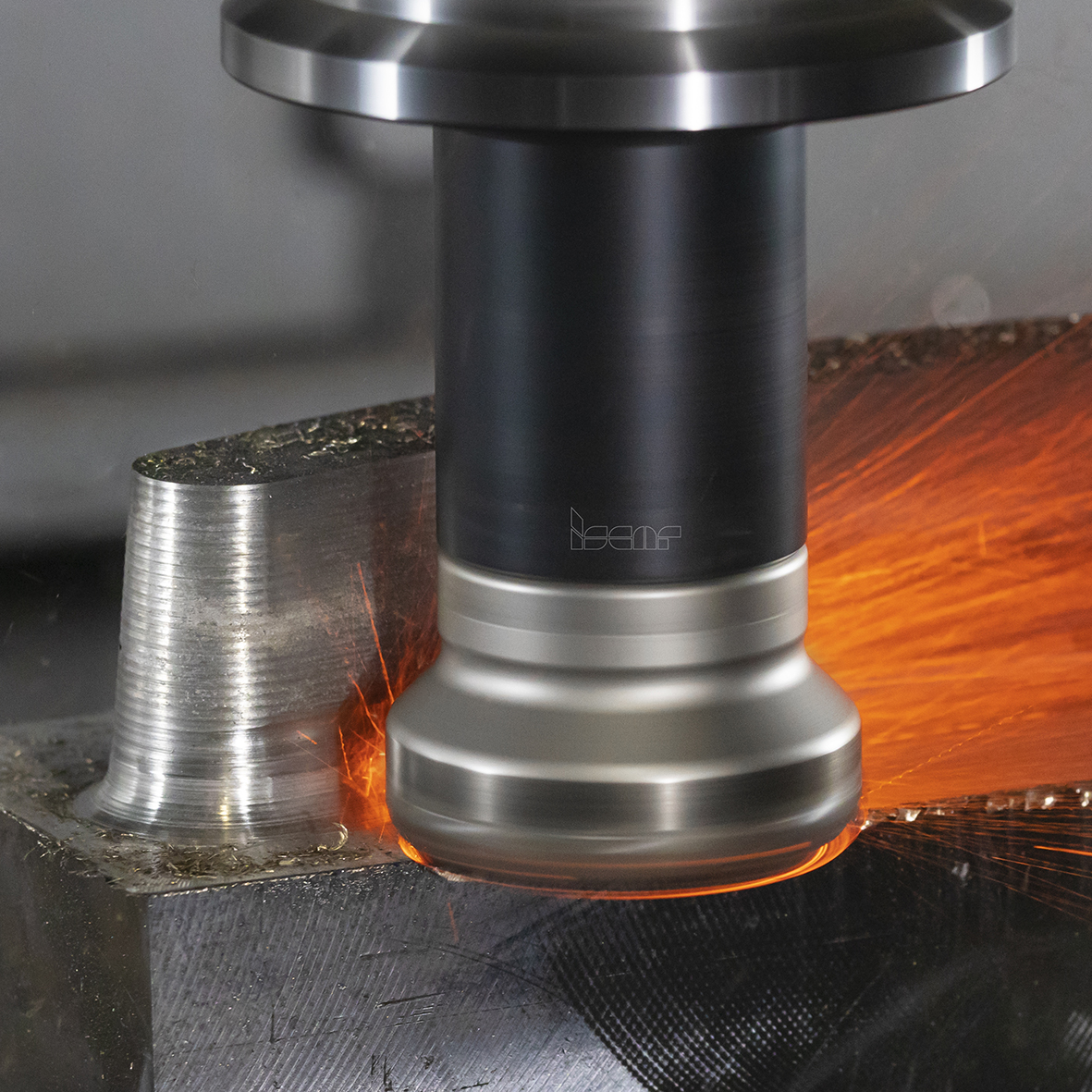
[Fig. 3- Milling cutters with indexable round inserts from ceramics provide considerably increased cutting speeds for higher productivity.]
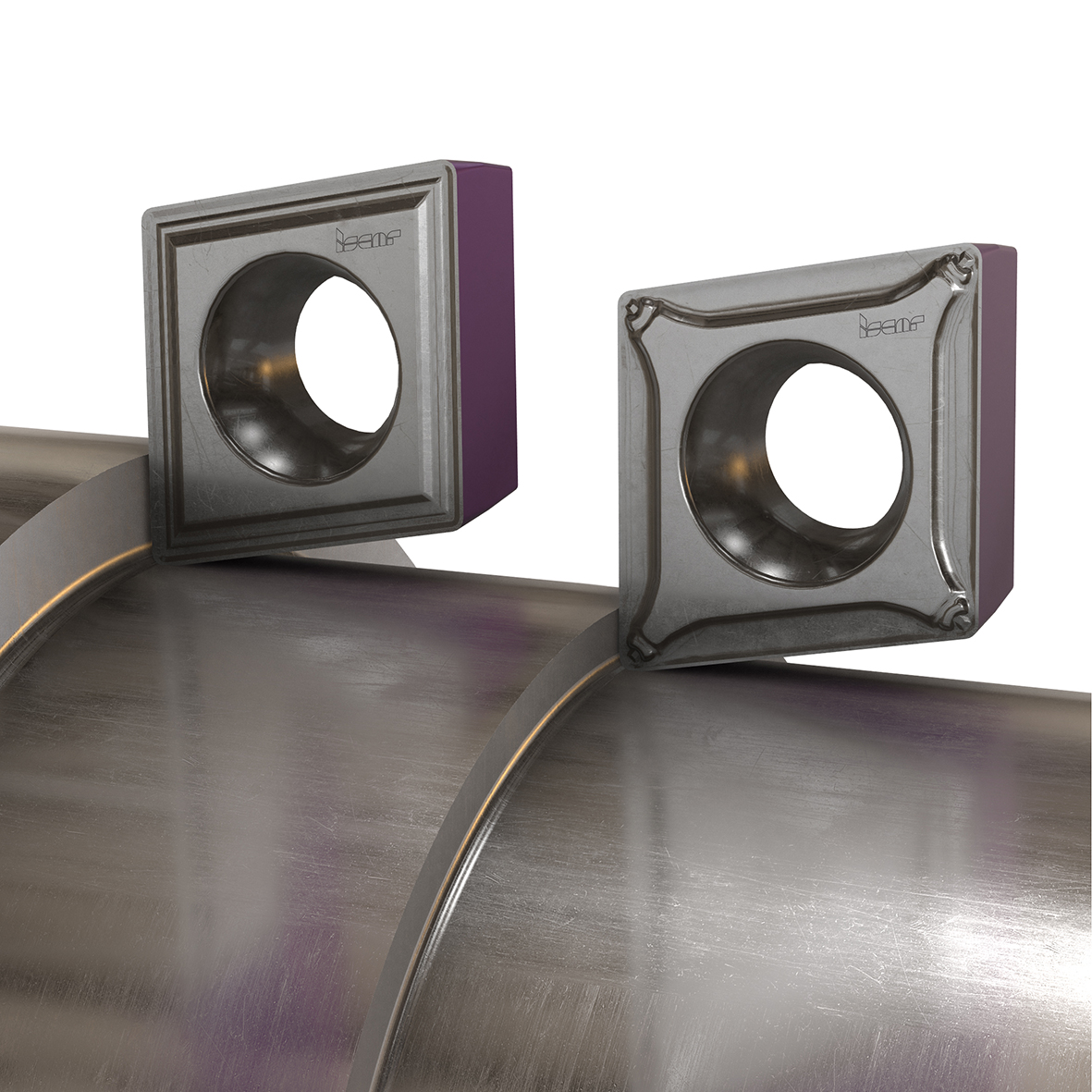
[Fig. 4- ISCAR’s recently introduced M3M (left) and F3M (right) chipbreakers for ISO standardized turning inserts designed specifically for ISO S and ISO M groups of application.]